FIMA Maschinenbau GmbH
Booth number: D124
www.fima.de/en
About us
FIMA Maschinenbau GmbH is a German manufacturer for single- and multistage radial blowers and turbo compressors. As a global player with offices in all key markets, we support our customers with our expertise to find the best individual solution. Our product range includes explosion-proof blowers for hazardous areas and gases as well as hermetically tight blowers and compressors. FIMA machines are available in many materials, e.g. stainless steel or titanium and according to common standards like DIN EN or the American API standard. Our products are used in almost every industry e.g. petrochemistry, chemistry and many more. The applications range from PP, PE, LNG, hydrochloric acid, formaldehyde, vapour to sulphur recovery units and CCR, only to name a few. Original spare parts and services are provided at all project stages by our own FIMA service team. Our service includes commissioning, maintenance, conversion, replacement machines and many more.
Address
Oberfischacher Str. 58
74423 Obersontheim
Germany
E-mail: info@fima.de
Phone: +49 7973 6930
Internet: www.fima.de
Contact person:
Products & Services
Radial compressors
Our radial compressors include single- and multistage process gas compressors, process air compressors and mechanical vapour compressors. In the integral version, the impeller is directly mounted on the highspeed shaft. Alternative versions are fitted with intermediate bearings. FIMA is the acknowledged future champion of the world market leader in low-volume radial/ turbo compressors. This type of compressor is frequently implemented in chemical processing plants or refineries.
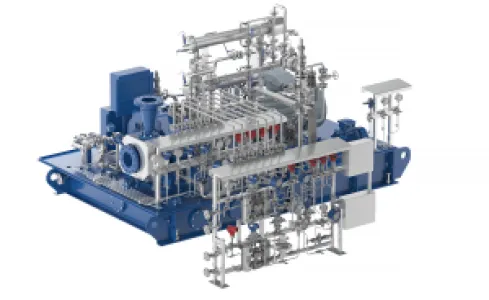
The plastic polyethylene (PE) is an extremely versatile product of the chemical industry. PE is used to make films of all kinds, beverage packaging, canisters, and even pipe jackets. The partially crystalline, nonpolar thermoplastic is divided up into different main types based on density. Through the selection of the polymerization conditions, the molecular weight, molecular weight distribution, kinetic chain length, and degree of polymerization are affected. Our F1 Series single-stage compressors are used in applications such as the licensed “Innovene G” process from Ineos for the production of linear low-density polyethylene (LLDPE). FIMA supplies the ejector boosters and the ethylene compressors for this process.
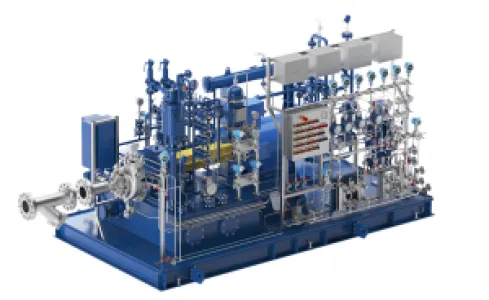
Compared with PE plastic, polypropylene (PP) is harder, is stronger, and can withstand higher thermal loads. Thanks to its special properties, PP has an extraordinarily wide range of applications. It is used in everything from vehicle interiors to food and cosmetics packaging, to pressure and drainage pipes. The licensed Novolen process from Lummus Novolen Technology for producing PP is just one example of the use of recycle gas compressors from FIMA. In general, these compressors return the unconverted propylene gas to the reactor. Smaller single-stage compressors are often used for homomer plants. So-called cascade compressors are also used in PP production. They are installed in the multistage variant.
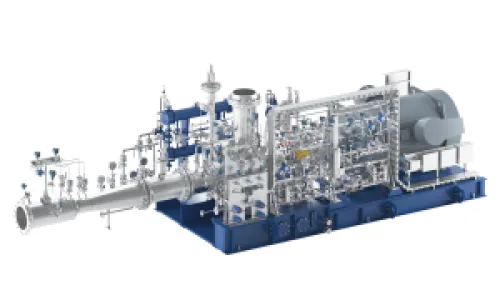
Hydrogen is one of the most important chemical elements and is a component of nearly all organic compounds. In response to the challenges of the energy transition, numerous new hydrogen-based processes are emerging, thereby building on the already significant role of hydrogen in numerous chemical processes. One example is oxo synthesis, also known as hydroformylation. The large-scale process is used to produce aldehydes. Hydrogen serves as one of the starting products of the process. The resulting aldehydes are usually hydrogenated to form alcohols and are ultimately used as plasticizers, raw materials for laundry detergents and cleaning agents, or solvents. Because the process gas has a high hydrogen content, the material’s resistance to hydrogen embrittlement by the medium poses a special challenge.
Turbo blowers & explosion-proof fans
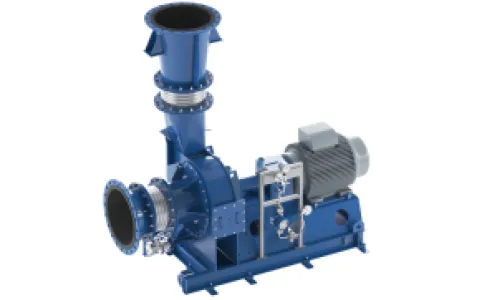
As chemical compounds from the group of aromatic isocyanates, methylene diphenyl diisocyanates are normally mixtures of several constitutional isomers. They differ in terms of the positions of the isocyanate groups. MDI is one of the most commonly produced isocyanates worldwide and is a key raw material for the production of polyurethane, polyamide and flexible foam, insulating foam, and adhesives. FIMA supplies single-stage radial blowers for the production of MDI. Products include containment, air extraction, and exhaust gas fans. The machines are manufactured from high-grade materials and realized in sophisticated designs.
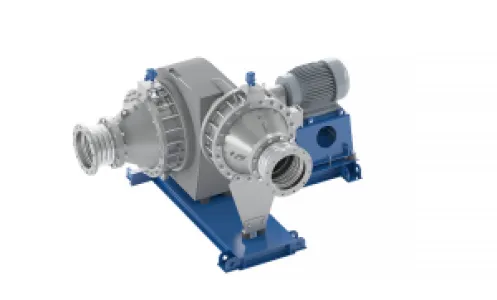
As world leaders (2010) in Zone 0 blowers, we are aware of the high risk associated with the conveyance of continuously explosive gases. In the conveyance of gases in Zone 0, the plant is constantly exposed to an explosion hazard. Thus, in light of this explosion hazard, safety is one of the most important aspects of our blowers. Our machines have type approval for explosion groups IIA, IIB, and IIB3. We cover T1–T4 temperature classes for the gas–air mixtures. Our blowers can be found in tank terminals as well as loading, exhaust air combustion, wastewater treatment, and flaring and landfill gas plants, among others.
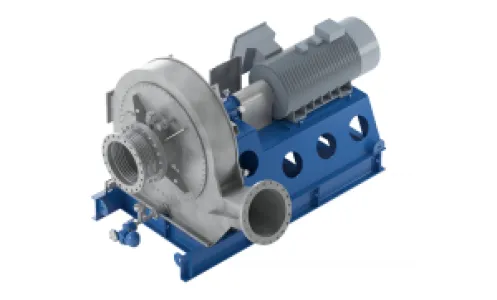
During the closed process of liquid evaporation, the vapor is fed through our VARECO, where its temperature and energy level are increased, and then fed back to the process. Thus, its valuable energy is not lost. The self-contained process allows volatile liquids to be evaporated while valuable products are retained. Our VARECO is used in the chemical industry in recovery processes for alcohols such as isopropanol and methanol. One example of its application is in the production of biofuels.
Hermetically encapsulated fans and compressors
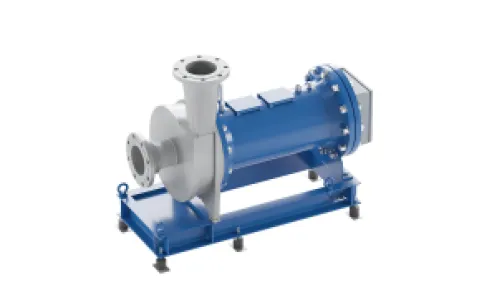
In the FIMA HETICO®, the impeller and the drive are both encapsulated in a single casing. In this way, dynamically loaded seals between the process area and the surroundings are avoided. The special gas-tight design of the HETICO® ensures that in applications with positive pressure, no process gas escapes into the outside atmosphere. Conversely, it prevents outside air from entering the process in vacuum applications. The explosion-proof design makes it suitable for use in explosive atmospheres and for conveyance of explosive media. It satisfies the requirements of Pressure Equipment Directive PED 2014/68/EU. The HETICO® is already being successfully deployed not just in laminate manufacturing, in thermal power stations, and in thermal exhaust gas treatment plants but also in satellite test beds. In a number of processes, it is used as a recirculation blower.

Due to the basic design of the magnetic coupling, the FIMA MACOUCO® is more environmentally compatible than conventional machine types are. In the MACOUCO®, the magnetic coupling and the bearing unit are flanged directly to the compressor housing, which is separated from the bearing unit through a gas-tight thermal insulation barrier. The hermetically sealed construction prevents dangerous gases from escaping into the environment. Without the need for dynamic seals, it is possible to obtain leak rates of less than 10-6 mbar*L/s with the FIMA MACOUCO®. Areas in which our MACOUCO® is used include polyolefin plants (catalloy, spherilene process), chlorine gas, regeneration, recovery, and recycling processes, and sterilization plants for surgical and medical instruments.